The SF02 milling truckOur all-rounder for Vignoles and grooved rails
Rail and switch maintenance can’t be done any more flexibly than this! The SF02 road-rail milling truck can be driven on public roads, so it can be deployed anywhere to provide solutions at small-scale works and support on large-scale projects. Why bring out the big machinery when you can correct rail defects in exactly the areas affected? In most cases, the SF02 W-FS covers the rail’s full profile in just a single pass. The milling truck’s strengths lie in the maintenance of grooved rails including the base of the groove and in the removal of corrugations. An integrated grinding unit does the fine grinding and ensures minimal residual roughness. The rail milling truck is environmentally friendly thanks to the minimal dust and sparks produced.
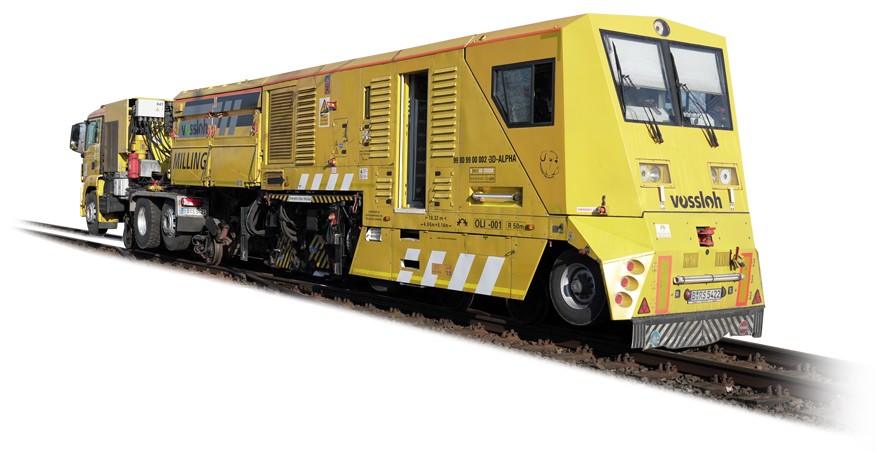
- Transport truck and machine in one
- Simple on-railing and off-railing
- No removal of trackside switching equipment required
- Short tooling times
- Wheel gauge can be changed from 1,000 mm – 1,520 mm at any time
- Machines both straight track and switches
- Preventive maintenance
- Removes rail-head defects in transverse and longitudinal profile
- Improves the ride and minimizes wear
- Noise reduction in sensitive areas
- Can correct track gauge by up to 5 mm (2 x 2.5 mm)
- Ideally suited to small-scale construction works and tram networks
One of the milling truck’s special features is the comprehensive switch machining
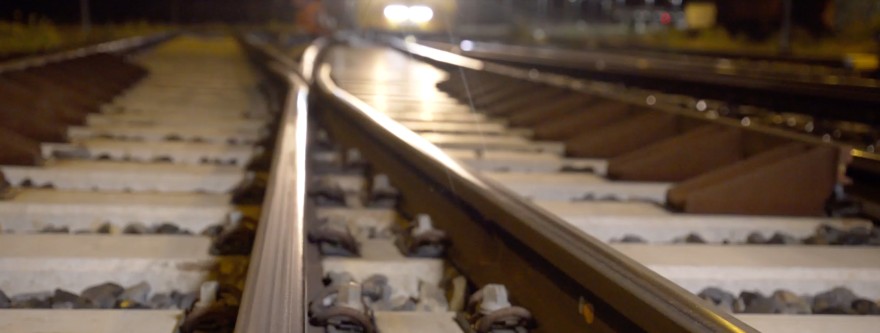
Milling a switch is a challenge and has not been given much consideration as a machining option until now. We can now machine up to 95% of a switch using a special tool – and that’s with DB approval and also on high-speed lines of up 280 km/h! The switch maintenance work is then completed using our Flexis system.
- Complete reprofiling including the frog, wing rails and point blades down to a blade-width of 20 mm.
- Minimal machining time required
- After machining the switch is reprofiled to near-new condition
Maintaining side-gouged rails in curved track
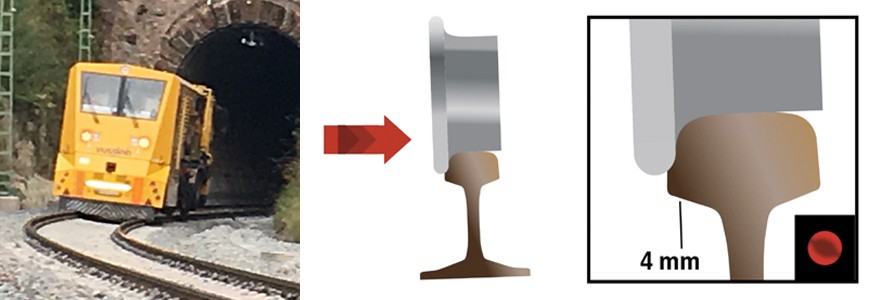
Over time, the centrifugal forces that occur when trains travel through curves produce a negative copy of the wheel profile in the gauge corner of the curve’s inside rail. Wear marks form which later become gouges in the side of the rail. With conventional milling tools, there’s the risk that the wheel flange will hit the bottom edge of the side gouging and consequently not rectify the defects in the running surface. After the profile has been corrected with the SF02 milling truck’s special tool, the rail can be machined again as normal and without any restrictions.
- Damage can now be milled out of rails that were previous regarded as beyond machining due to severe side gouging
- A specially-designed milling wheel displaces the critical zone along the bottom of the gouge approx. 4 mm lower down
Track-gauge correction
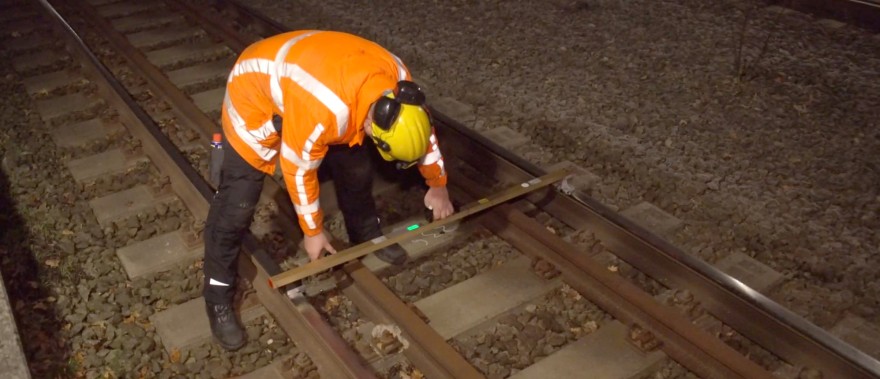
Various circumstances can cause the track gauge to narrow in places, which can lead to the track having to be closed. Proper track gauge correction using the SF02 milling truck quickly ensures safe, long-term operation.
- Prevents tracks from being closed to rail operations
- Prevents premature wear of the wheel tyres on vehicles
- Reduces noise
- Increases operational safety
Maintenance of grooved rails
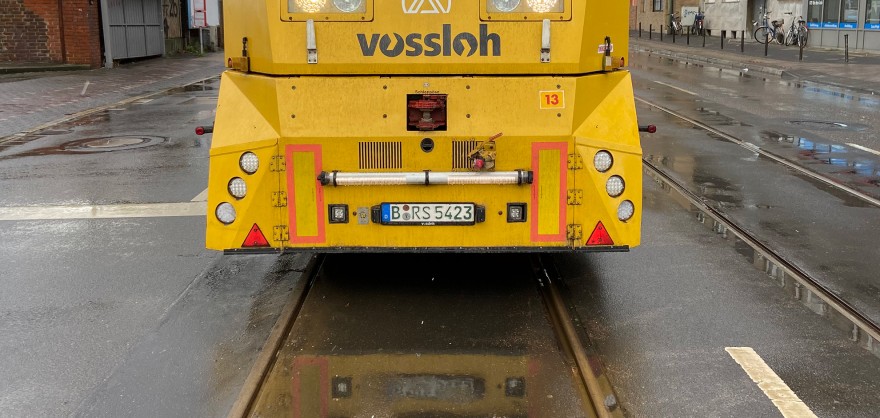
Up until now it hasn’t been possible to correctively machine grooved rails without removing the sealing compound along the rail’s outside edge. Our SF02 road-rail milling truck has a special tool that is equipped with additional cutting tips on both sides of its wheel flange, which for the first time ever makes it possible to rectify defects in a single pass.
- First comprehensive corrective machining of grooved rails
- Efficient use of track possession thanks to quick on-railing and off-railing
- Several hotspots can be accessed by road in a single shift
Maintaining rails with gauge corner damage deeper than Z-14
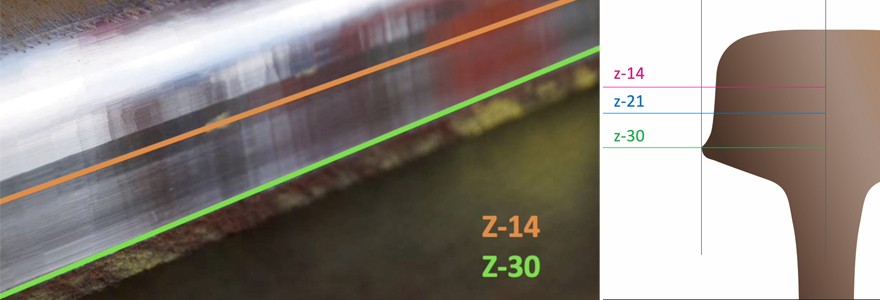
A cutting zone that extends along the gauge-face side of the milling wheel allows it to machine down to Z-30. If, for example, vehicle wheels with different flange heights varying between Z-25 and Z-28 are used, this can cause a sharp lip to form on the rail's gauge face, which in turn damages wheels with larger wheel flanges. Our milling wheel profile mills beyond the required Z-21, so it can also be used to correct gauge narrowing.
- Defects in the gauge face of the rail below Z-21 can be fully machined using our special milling tool
- The full rail-wheel contact surface is completely machined
- Replacing the rail is not necessary
Our SF02 road-rail milling truck – Your problem-solver!
Contact us. We’ll come and inspect your track together with you and then get things under way!