Flexis System
The rail-reprofiling machines that make up the Flexis System …
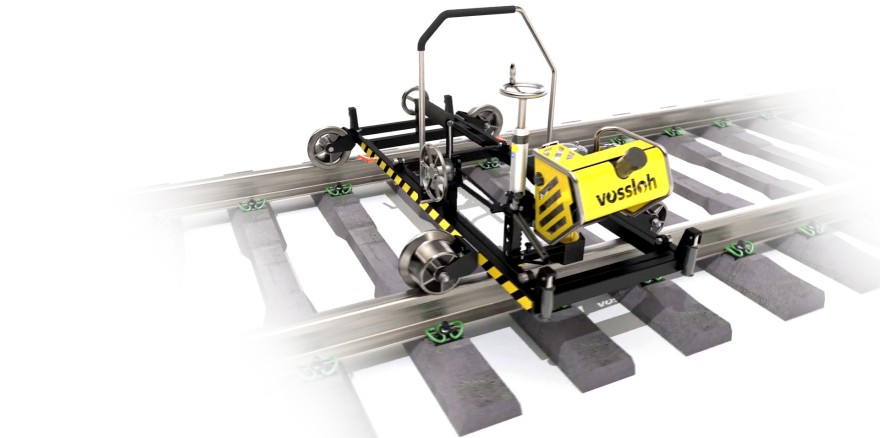
- Flexis machine (gauge corner / transverse profile)
- corrugation machine (running surface / longitudinal profile) and the
- deburring machine
… are all rail-guided, which results in uniform longitudinal and transverse machining along the whole track section
(as per EN 13231:3-2012). Low contact pressure ensures there are no grinding marks or heat-induced changes to the material properties, and every machine can be adjusted to the track gauge required. The versatility of the system is demonstrated by the fact that it can machine every rail type and every rail profile. Across Europe, Flexis is ideal for customers from areas as diverse as state-owned high-speed lines, classical main line routes and light rail transit.
Hot-spot machining
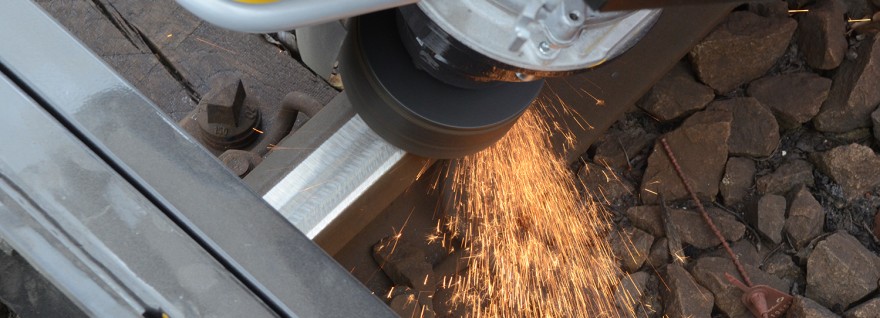
Efficient hot-spot machining removes wheel burn as well, which is commonly regarded as a type of isolated defect. Wheel burn occurs on gradients ahead of signals or on track sections where vehicles often have to stop before getting underway again. The versatility and independence of the Flexis machines enable speedy removal of isolated rail defects such as squats, indentations or sharp-edged weld seams.
Rail expansion joints
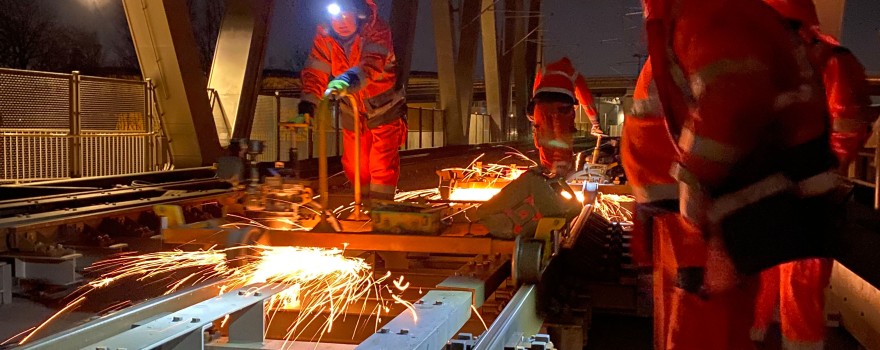
The way that rail expansion joints are constructed makes them particularly challenging for heavy rail-reprofiling machines. Milling machines cannot machine them at all and rail-bound or road-rail grinding machines are only able to machine them with difficulty. What’s more, this entails:
- complex logistical requirements such as delivery and retrieval of the vehicles, and
- a track closure for a relatively short section of track.
Customized and mobile, the operational alternatives offered by Flexis allow rail expansion joints to be machined quickly without complex logistical requirements and in full compliance with regulatory requirements.
Level crossings
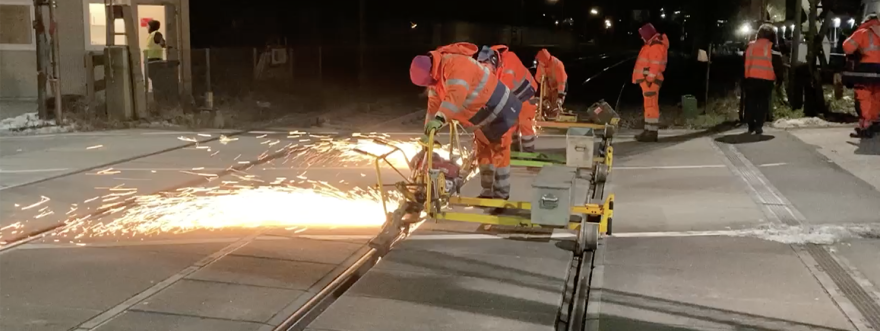
The winter months are particularly hard on the running surfaces of the rails at level crossings. In order to ensure that traffic can be cleared quickly when trains come, a lot of grit is put down in and around level crossings. The road vehicles distribute this grit over the crossing, and some of it comes to rest on the rails. The next train to go through the crossing causes severe damage to the rails in and around the area. Individual pieces of grit can get caught in the rail tyres and damage both the wheel and a lengthy section of the track. Thanks to the accessibility by road, Flexis can quickly machine out rail damage in and around asphalted level crossings.
Rail machining
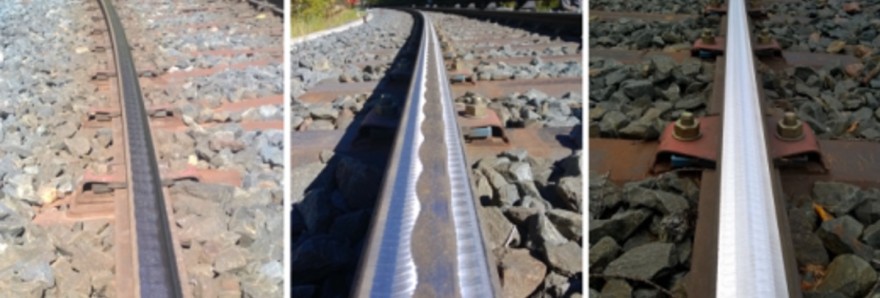
1. Condition of rail before machining
2. Rail during machining using the Flexis System
3. Rail after being machined using the Flexis System
Easy to use
Flexis combines adequate machining with cost-effectiveness. When the track possession begins, the machines are quickly on-railed at the location that needs machining. Flexis can be used effectively during track possessions as short as ten minutes, and consequently does not interfere with the rail network's operations. The system complies with the maximum off-railing time of 20 seconds as specified in the statutory accident insurance regulations, which allows Flexis to machine rails quickly and easily and without the need for dismantling any trackside switching equipment.
Comprehensive switch machining
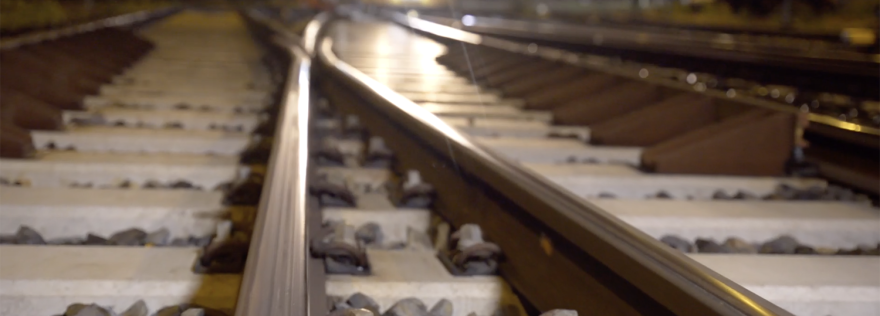
In keeping with the uniqueness of every switch, the team considers every area of a switch as a distinct entity and machines every component according to the requirements of that component. The cup wheels on the machines are adjusted to the right position in order to be able to machine the entire rail head from the running surface to the gauge corner until the desired geometry is achieved.
The number of machines and operators the Flexis System will require can be adjusted and planned out in advance to suit the scope of the work commissioned. Larger teams are often requested for the preparatory machining of new switches, or when switches with radii in excess of 1,200 m need maintenance. On average, it takes around three hours to machine a new switch with a radius of 300 m. Increasing the number of operators in the team can reduce the time needed to machine a switch by as much as 40%.
As manual grinding using Flexis would then be reduced to a minimum, combining the Flexis System with a milling truck can considerably shorten the machining time for switches requiring more than 0.5 mm of metal to be removed. This method allows several switches and the various rail lengths connected to them to be machined in one shift.
Complementing heavy rail-reprofiling machinery
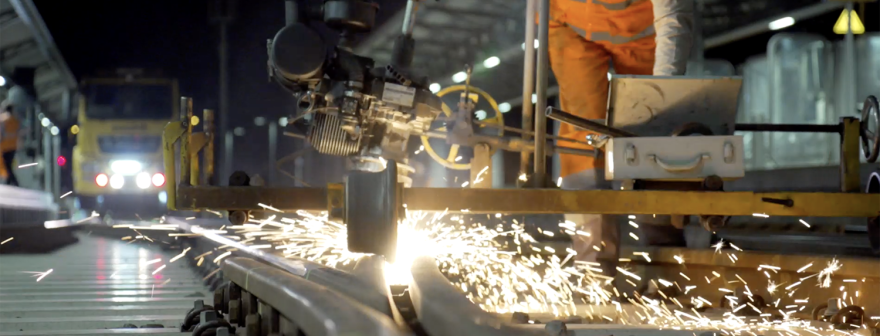
Minimal costs associated with operational complications and simple logistics make Flexis the perfect complement to heavy rail-reprofiling machines, which focus on achieving high output. Sharing the work with larger machines pays off on shorter track sections where Flexis can level out the transition points to switches and insulated joints. On the other hand, there are also situations where using large machines to reprofile the track is either impossible or uneconomical. Single-slip and double-slip switches and crossings, for example, are difficult to machine because of the nature of their design. “Real craftsmanship” is also the order of the day when machining common crossings with lower points or elevated wing rails, and the same applies to rail expansion joints.
Thanks to its versatility and mobility, Flexis is up to the challenge of reconditioning these components as per regulatory requirements – and all without any logistical expenditure at all.
Suitable for steeply sloping track
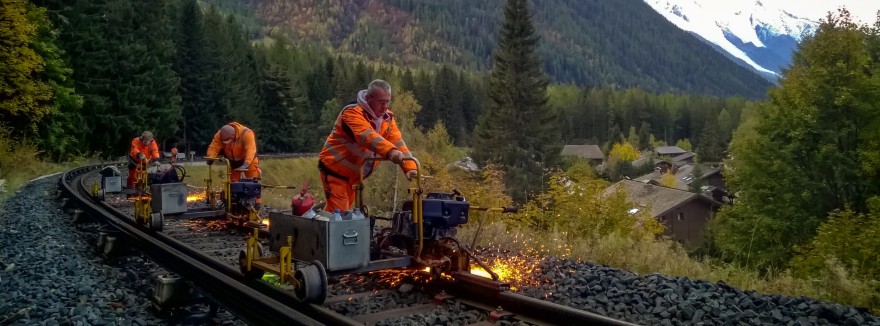
Track sections with longitudinal gradients of more than 40 ‰ – like the Mont-Blanc Express in France – are classified as "steeply sloping track", and conventional rail vehicles are not permitted to use them without meeting additional requirements (e.g. additional brake locomotive). The autonomy of the Flexis System allows it to machine the rails of even the steepest pinion-less railway line in Europe on extreme gradients of up to 90 ‰ at no great expense.
Needs-based, high-quality machining
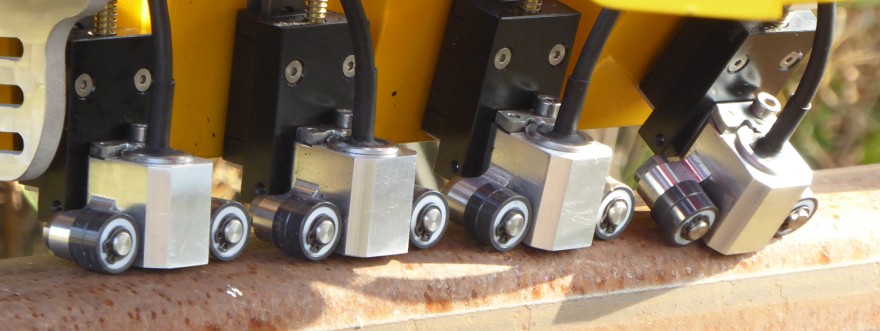
In order to keep the required material removal to an absolute minimum, precise measurements as per EN 13231:3-2012 are performed on the switch before starting any machining work. In addition to measuring the longitudinal and transverse profiles, the standard process involves detecting head checks using eddy-current technology. Material removal as the difference in height along with surface roughness are also measured and included in the work documentation to demonstrate compliance.
Grooved rails aren’t a problem
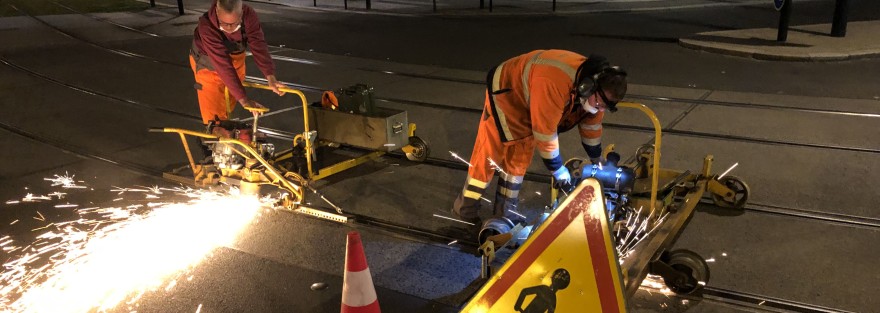
Of course, the Flexis System can also be used on grooved rails in light rail networks.
Our Flexis System is the solution to your problems!
Contact us to arrange a track inspection. Once we’ve assessed the condition of your rails together with you, we can get started right away!